Learn how Moriwaki Engineering Co., Ltd. increasingly relies on 3D laser measurement technology by FARO to scan and probe small parts in the development, design, manufacture, and sale of motorcycle mufflers and other high-performance parts.
Original Source - FARO Technologies
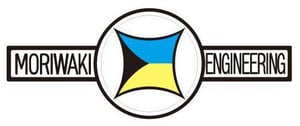
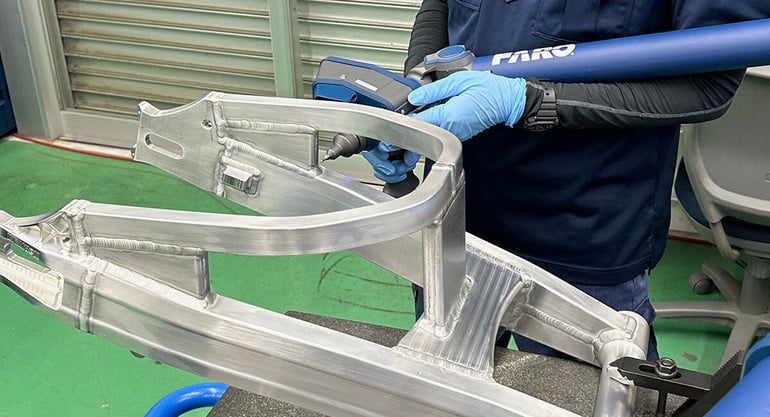
For nearly 75 years Japanese motorcycle culture has been known around the world. Often, these brands rival and, in many cases, surpass, the best of what other nations can achieve.
As a top 20 nation for motorcycle ridership, Japanese bike culture is widely associated with freedom, individuality, tolerance, and progressivism. Today approximately 10.3 million motorcycles are owned across the country, with the primary market dominated by smaller engine vehicles, particularly those under 50 cc. Less well known, however, is the critical parallel industry of parts production and accessories manufacture. And by extension, the measurement technology required to build, retrofit, and repair those motorcycles as needs dictate.
One such company is Moriwaki Engineering Co., Ltd. Founded in 1973, Moriwaki Engineering specializes in motorcycles and cars, including the development, design, manufacture, and sales of motorcycle mufflers and other high-performance parts. Based in Suzuka (Mie Prefecture ) the brand operates nationwide, has a professional racing component, and exports to dozens of markets, including the United States, Europe, Asia, and Australia, among others. To live up to the company’s slogan “Beyond the Best,” Moriwaki has for the last two decades relied increasingly on 3D laser scanning technology.
When Every Second and Every Millimeter Count
Primarily this has meant portable scan arms designed to measure parts with high accuracy – without having to move a part to a fixed CMM. Moriwaki’s journey with FARO began in 2002, upgrading their arms as the technology evolved. First, with the FaroArm Gold, continuing with the FARO Edge ScanArm, and most recently with the purchase of a FARO Quantum Max. The Quantum Max upgrade was principally pursued to improve scanning accuracy and reduce measurement & data preparation time, as well as reverse engineering and quality control.
“The Quantum Max is an indispensable tool in Moriwaki’s manufacturing process,” said Moriwaki’s Koji Takahashi, Manager, Design Development Section, Engineering Department. “With the FaroBlu Laser Line Probe an entire bike can be scanned smoothly without changing settings. Additionally, the ability to get all the data cleanly facilitated makes communication between departments and downstream development and design work easier.”
The “before and after” difference is what sets 3D scanning apart from traditional measurement methods. Prior to the use of an portable arm manufacturers relied on calipers, circumferential gauges, protractors, and related analog tools. In designing a muffler, for instance, the layout is determined by connecting the pipes together on the actual motorcycle, and from that, a master model is created. Jigs are then fabricated from that master model. This was a time-consuming, error-prone process, with a variety of additional limitations, chiefly in terms of 3D data acquisition, repeatability and quality control.
With scanning tools like the FaroArm, many of these challenges were eliminated. One of the greatest advantages of working with FaroBlu, (the laser line probe) is the ability to create CAD designs and use numerical control machining. With traditional measurement tools, 3D data is not possible.
Since custom parts are not created with a 3D model, a manufacturer must create a master model physically using the motorcycle itself, additional verification and development work is almost impossible after the motorcycle is returned. Nor is it possible to determine numerically whether an item is completed according to the master model. Last, since the original (master model) is the authentic one, it cannot be reproduced if it is lost or damaged, or in the case of an entire motorcycle, be returned to an owner. By contrast, 3D laser scanning creates a virtual 3D model that can be constantly compared to the physical part.
The Quantum Max only enhances these scanning capabilities.
“The Quantum Max is a more compact scanner than the competition, and the kinematic mount allows the LLP to be mounted in two different locations,” - Takahashi explained.
“To scan the underside of a motorcycle, the LLP must be repositioned. The FaroArm is compact and can be mounted in two positions without re-calibration.”
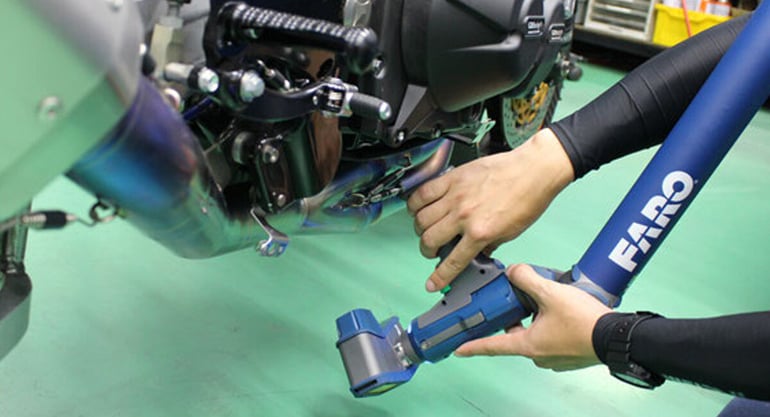
Thanks to the Quantum Max improvements Takahashi estimates that the time required for the entire process, from measurement preparation to actual measurement, to data editing, was reduced by 50% compared to previous LLPs.
The Need for Speed - And Simplicity
Another benefit of working with the Quantum Max is its ease of use. FARO enables a seamless ramp-up, providing equipment setup, live demonstrations, model selection, product quotes, and delivery – even though there was time pressure for Moriwaki Engineering to install the FARO equipment.
As is often the case with any new technology, use cases expand as comfort using the product and versality awareness increase. In addition to scanning individual parts like mufflers, Moriwaki today scans entire motorcycles. The FAROBlu laser makes it possible to scan parts of different materials and colors at once without having to change settings, so scanning an entire motorcycle can be completed in a short time. Although the measurement work itself has increased, the work afterwards, like designing, has become easier, and there is less rework, waste, and scrap.
Takahashi also praised the FARO CAM2 Software, which requires less process time until measurement results are obtained and features an easy-to-understand operation system. Perhaps most useful is the fact that CAM2 is designed for use with any FARO coordinate measuring machine, enabling operators to capture accurate measurements with a world-leading 3D measurement platform and future-compatible with any upcoming release.
“We have been focusing on motorcycle racing activities for many years and have taken on various technical challenges,” added Takahiro Ochi, Chief, Design Development Section, Engineering Department. “We have been able to continue to provide high value to our customers by feeding back the technical capabilities they have gained through these efforts to their products. FARO products have played an important role in improving our technical capabilities and are indispensable for our company to continue taking on various challenges in the future.”
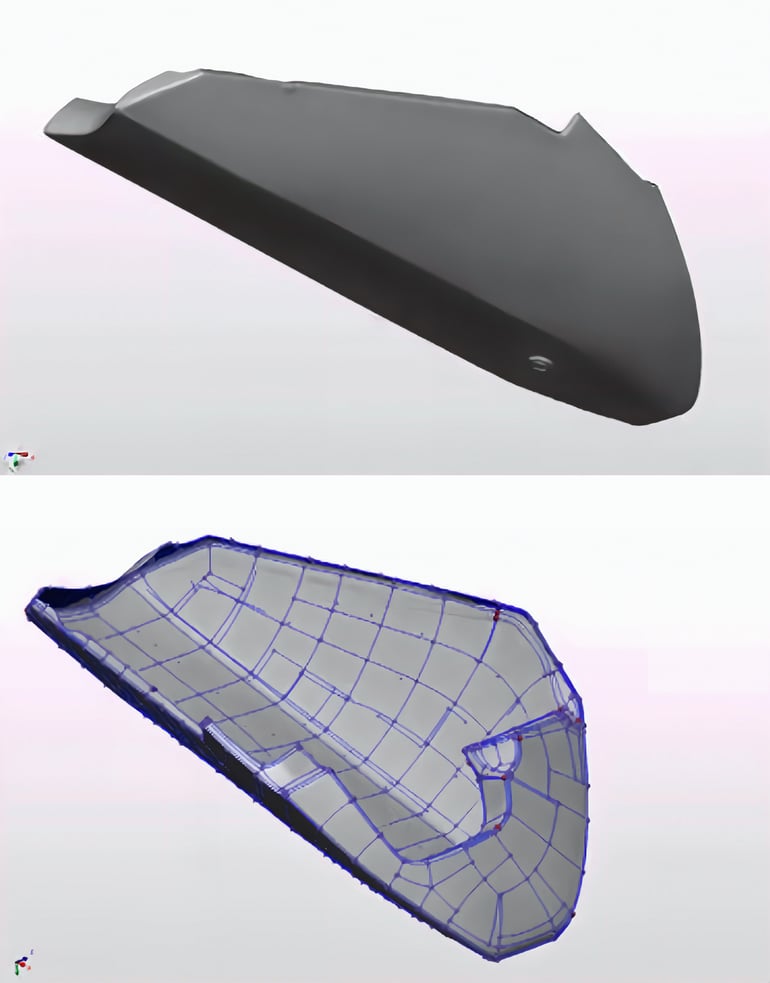
Two-wheeled Industry Rebound
In the last few decades, Japanese two-wheeled personal transportation has taken a hit. Excellent mass transit and motorcycle safety concerns have also eroded some of their historic popularity.
Following the global pandemic in 2020, however, demand for motorcycles recovered somewhat due to lingering fears of crowded spaces, as is common on mass transit. There’s likewise been a rebound effect as “return riders” rediscover the fun and utility of such travel.
But if total ridership numbers are down, the diversity of Japan’s two-wheeled market remains robust. Motorcycles are just one component of a personalized transportation space that includes bicycles, e-bikes, scooters, and mopeds. Regardless of which method of transit is used, all vehicles must be manufactured with tight tolerances to ensure product safety and public embrace.
Whether it’s designing a muffler or any other motorcycle part, or it’s inspecting and manufacturing the small and medium-sized components built into the millions of
two-wheeled vehicles on Japan’s roads, technology like the FARO Quantum Max and future products, will continue leading the way. Collectively they help manufacturers like Moriwaki Engineering make the transition from traditional measurement tools to advanced portable 3D scanning devices that can in minutes, convert a physical object into a digital, sharable replica.
To learn more about about our New Quantum X FaroArm Series
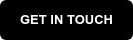