SKI decided to implement Nexa3D Freeform Injection Moulding to offer shorter lead times on complex injection moulded parts in challenging materials. At the same time, SK Industriemodell saw an attractive opportunity to supply injection-moulded parts in quantities that would normally be too low for conventional injection moulding due to the costs of tooling. Spare parts on demand is one of the most interesting applications for this kind of manufacturing model and one that is well suited to the unique design freedom and selection of materials offered by Freeform Injection Moulding.
Original Source - Nexa3D
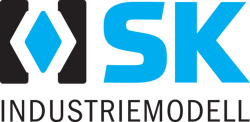
The Customer
SK Industriemodell (SKI) is a fully integrated provider of development and manufacturing services to customers in the automotive, medical device, and other demanding industries, with almost a decade of experience with the use of 3D printed injection moulds. Boasting a fully-fledged tool shop, and with extensive experience in lead-time compression, they provide product development support as well as manufacturing services to a large number of companies in northern Europe.
INDUSTRY
Vespa Vintage Community
PRODUCTS
XiP Desktop 3D Printer
xMOLD 3D printed tooling resin
APPLICATION
Spare Parts Manufacturing
ADVANTAGES
- Validated high-performance materials readily available
- Part quality on a level with conventional injection moulding, without investments in moulds
- No minimum order quantities – injection moulding on demand enabled
- Lighter weights, lower costs achievable by use of polymers instead of metals
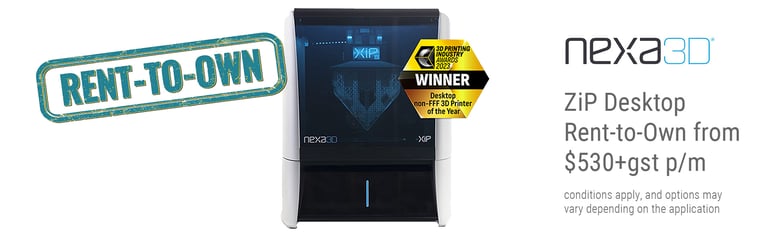
The Challenge
Complex fan wheel for high-temperature application needed in low volumes
Vespa, an Italian luxury brand of scooters and mopeds manufactured by Piaggio, has gained a very large following, and some of their vintage models are in high demand because of their bold designs and unique driving experience. However, wear and tear eventually results in the need for parts to be replaced, and owners sometimes struggle to find qualified spare parts.
One of the more challenging parts is the air fan that rams air into the Vespa engine compartment to cool the engine. This fan runs at high speeds while being exposed to temperatures up to 80 degrees C as well as salt spray, dust, and a number of other stress factors resulting from outdoor use.
In the spring of 2024, SK Industriemodell was approached by members of a local Vespa community looking for ways to source spare parts for Vespa vintage models. First among the sought-after parts was the air fan, and the community had evaluated a range of low-volume manufacturing alternatives without finding a solution that would offer the desired combination of cost, performance, and quality.
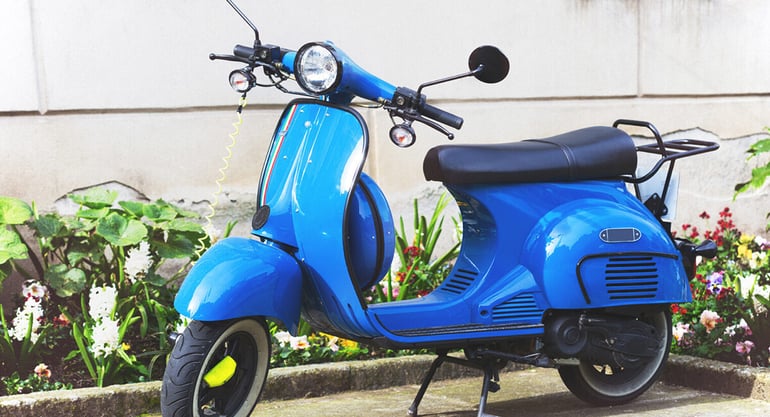
“Freeform Injection Molding has enabled us to expand the use of injection molding into low-volume applications normally reserved for milling and 3D printing while still offering the quality, versatility and scalability known from injection molding.” – Sebastian Krell, CEO, SK Industriemodell
The Solution
Freeform Injection Molding Enables 3-Piece Batches in Field-Validated Material
SK Industriemodell is an experienced supplier to the automotive industry, where high heat tolerance is important for engine compartment parts. PA6 GF30, a glass-filled nylon, is one of the industry gold standards for these applications, and SKI decided for this particular polymer to provide the needed combination of strength, heat resistance and durability. Freeform Injection Molding was selected as the manufacturing method, due to the complex design of the air fan and the customer’s need for on-demand injection molding of small batches. Printing of moulds was done on the Nexa3D XiP desktop 3D printer, with the xMOLD soluble tooling resin providing the needed design freedom. The first injection-molded parts were provided to the customer less than two weeks after receipt of the first order.
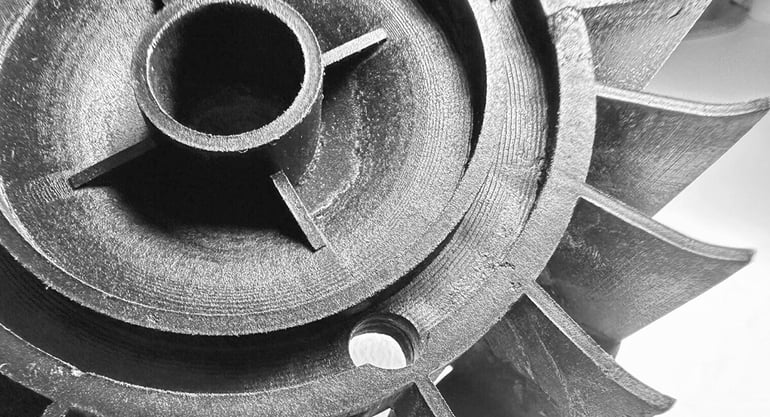
Benefit
Complex spare parts injection-moulded on demand in validated material
With Freeform Injection Molding, SK Industriemodell was able to supply spare parts on demand, in a quality that met demands for high heat tolerance and durability, at an acceptable cost level.
No Minimum Order Quantities
Freeform Injection Molding is ideal for low-volume injection moulding due to its unique combination of simplicity, versatility and easy run-in. The first batch of 3 parts was produced with 5 shots, including the two shots needed to dial in the parameters for the first round of moulding. Once parameters have been dialled in, subsequent productions will require no run-in of moulds or parameters.
Design Freedom
The soluble xMOLD tooling resin used in the Freeform Injection Moulding process enables the injection moulder to sidestep the cores, sliders and other mould action normally required for the moulding of complex parts, and which drive up the cost, complexity and lead time on conventional injection moulds.
Versatility
Another key benefit of solubility is that even materials that will normally tend to adhere to the mould surface can be easily de-moulded. xMOLD soluble tools have been successfully used in the injection moulding of the entire range of thermoplastics, as well as metals, ceramics, silicones and a number of other thermoset materials.
Precision
Freeform Injection Molding exploits the precision and high surface qualities available from resin printing, combined with the repeatability and process control from injection moulding. This combination resulted in the air fans being usable straight out of the tool, with no post-processing needed before assembly into the engine.
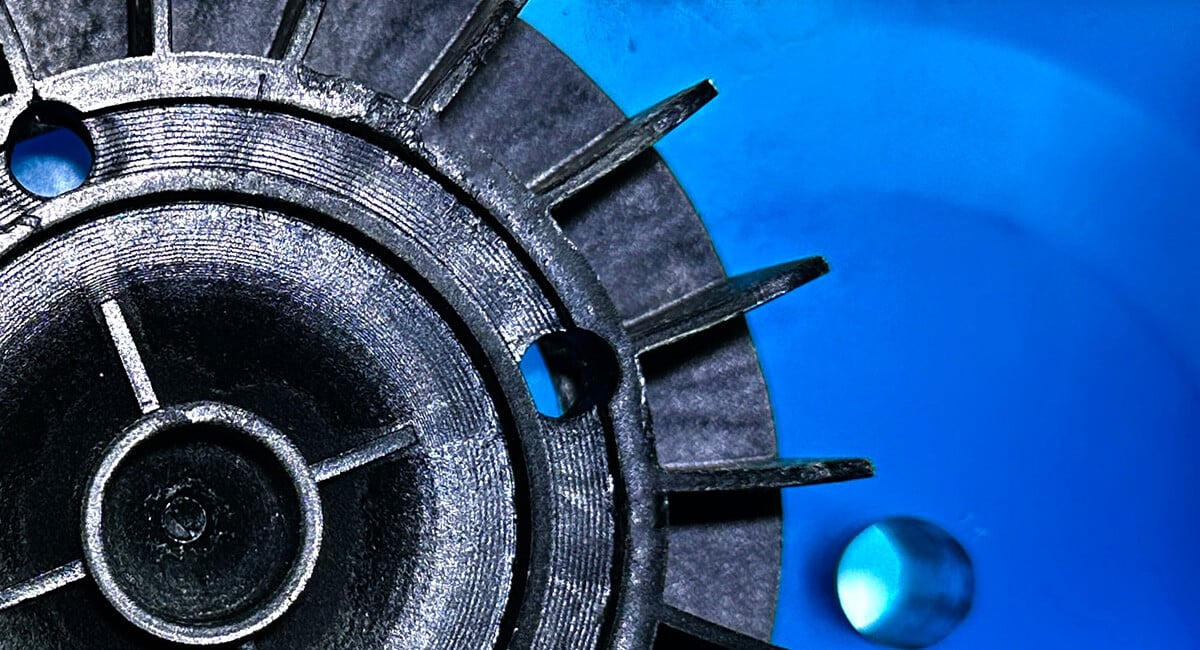
Customer Impact
Supply of injection-molded spare parts on demand enabled
The supply of spare parts is one of the most challenging fields in the manufacturing industry. Suppliers will either have to warehouse large numbers of parts to ensure availability, or alternatively develop on-demand manufacturing solutions where such solutions are able to comply with part performance and other requirements.
SK Industriemodell was able to leverage Freeform Injection Molding to produce spare parts in a heat-resistant engineering polymer that has an established track record in similar applications. The parts produced met performance and quality requirements and enabled SKI to start supplying cost-competitive air fans to a large base of dedicated customers.
At the same time, SK Industriemodell has demonstrated how xMOLD 3D printed moulds allow injection moulders to leverage injection moulding for the manufacturing of complex items in ultra-low volumes that would normally be entirely outside the domain of injection moulding. This has enabled SKI to expand the range of injection moulding services offered into the domain of spare parts on demand, a very significant business opportunity for the company.
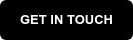