Steam Factory LLC in Saint Paul, Minnesota, offers highly customisable design, engineering, manufacturing, and 3D printing services, working to make 3D printing technology accessible to all. Rick Beddoe, Principal Engineer and CEO of Steam Factory takes on a range of projects, working with customers to make their ideas a reality. A Formlabs user since Form 2, he currently prints on 15 different 3D printers, 10 of which are Formlabs printers including Form 4, Form 4L, Form 3+ Form 3L, and a Fuse 1.
Original Source - Formlabs
The vRad® Grip is a project Beddoe started in 2023 for vRad®, a company offering radiology services. The vRad Grip is a highly customised controller for radiologists with an ergonomic design and two sizes. Beddoe began by printing the end-use device on Form 3 and Form 3L, but over the course of 2024, transitioned manufacturing to Form 4 and Form 4L. By upgrading from Form 3/L to Form 4/L, Beddoe was able to increase throughput by more than 4x and decrease cost per part by 10-15% — all with shortened lead times and lower costs than manufacturing via injection molding.
3D Printing vs. Injection Molding
Decreased Costs and Shorter Timelines
The vRad® Grip has an ergonomic form — it’s organic, requires space for buttons, and consists of two 3D printed parts. Stereolithography (SLA) 3D printing can easily produce organic forms with complex geometries and small openings, making it ideal for parts such as the vRad® Grip.
vRad® wanted an initial safety stock of ~500 units, followed by 30-40 units a month. The tooling needed for injection molding would likely have been made overseas and a quote came in around $70,000. This would be cost-effective for higher volumes — in the 100,000 piece range — but this was a much greater volume than was required and meant vRad® would be locked into a single design. New products change with feedback from end users. Having design flexibility enables vRad® to apply this feedback and improve the product over time.
Beddoe says, “The major time savings has to do with lead times.” For injection molding, orders would need to be put in 2-3 weeks before parts were needed, and an initial order could take 3-4 months due to the time it takes to create the mold. By contrast, 3D printing parts would take hours at most. Beddoe says, “Injection molding loses when talking short runs. By using the Formlabs equipment, we could keep all fabrication local to the customer, for decreased lead time and greater control over production.”
Printing with Formlabs SLA 3D printers also means Beddoe can achieve the smooth surfaces and tight tolerances one would expect from injection molding.
“For us, the appearance is very important. We actually print a 'leather-like' pattern into the part along with a knurled pattern to give it texture. Smooth parts are great, but the resolution on the Form 4 is so good we can capture subtle details like grain in leather.” Rick Beddoe, Principal Engineer/CEO, Steam Factory Design and Development
Part Set-Up
Developing the part was not without hurdles. Producing end-use parts with SLA 3D printing requires that the parts be optimally set up, including part orientation, and supports that assure a successful print placed on surfaces that do not need to look pristine. Beddoe uses PreForm, Formlabs’ print preparation software, to set up parts for printing. He says that “the biggest challenge for the vRad® Grip was getting the geometry just right on the build platform.” This involved adjustments to the file design in CAD before importing it into PreForm to print. Additionally, “we did not want a bunch of support artifacts on the ergonomic surface.” Finding the optimal part orientation, and adding texture to the surface ultimately “worked out extremely well and the devices look very good now,” says Beddoe.
“PreForm improvements made it easier to identify potential problem areas. We also added additional structures inside the part. Eventually, we had everything working perfectly. We have successfully delivered around 300 units with very few, if any, failures. Especially on the Form 4/4L.” Rick Beddoe, Principal Engineer/CEO, Steam Factory Design and Development
Enabling Customisation
“One of the biggest benefits of 3D printing is the ability to change the design at any time. These can be subtle changes like adding additional internal features for making assembly more efficient or changing the texture. We are able to make any changes they need without any interruptions in manufacturing.” Rick Beddoe, Principal Engineer/CEO, Steam Factory Design and Development
An additional benefit to 3D printing became apparent when the buttons for the vRad® Grip faced major increases in lead time. Beddoe was able to revise the electrical component and 3D print the buttons. He says, “This actually reduced our part cost considerably and gave the device a much better appearance.”
For the vRad® Grip, full advantage was taken of the ability to customise parts. This includes a part and version number, plus a quote that is printed on the bottom of the device. Additionally, vRad® Grips can be produced for different sizes of hands, and for lefties, which many companies forgo due to the cost of producing molds.
The Benefits of Upgrading to Form 4 Series 3D Printers
The exterior of the vRad® Grip is printed on Formlabs 3D printers. Beddoe has found that it costs 25% less to print on Form 4L than Form 3L.
Beddoe began production of the vRad® Grip on Form 3 and Form 3L. But upgrading to Form 4, and later Form 4L, he found that he could increase his throughput not just due to the increased print speed of the Low Force Display™ (LFD) technology, but also due to the larger build volume: Form 4 has 30% larger build volume than Form 3+, while Form 4L boosts a 13% larger build volume than Form 3L. This increase enables Beddoe to place more parts in a single build, for significant increases in throughput.
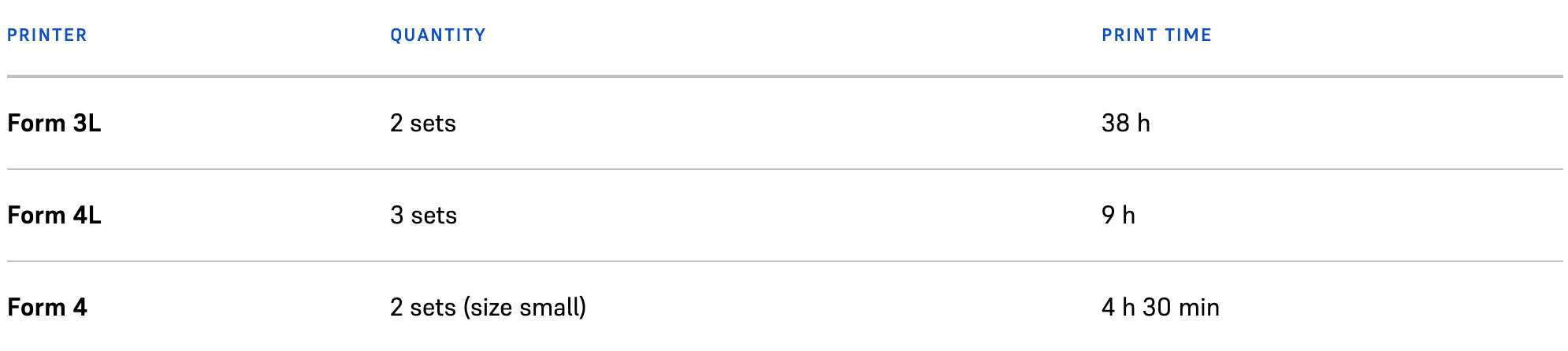
Lower Costs and Finer Finishes With New Resins
“The new materials are phenomenal. The new Clear Resin V5 is water clear and very cool once polished.” Rick Beddoe, Principal Engineer/CEO, Steam Factory Design and Development
The release of Form 4 opened up the opportunity to develop resins optimised for printing on the new hardware, including new General Purpose Resins. In addition to Clear Resin V5 being clearer and less yellow than Clear Resin V4, Beddoe says, “Black V5 is darker. It also has an interesting sheen to it that you can only see when the light hits it just right. Gives it a much higher-end look. It also seems to clean up better in the wash than V4. I don’t need as many supports with V5 and the touch points are smaller which makes the supports easier to remove.”
In addition to aesthetics, the cost of V5 General Purpose Resins start at $79/L, with additional discounts available for bulk orders. This means that printing on Form 4 Series 3D printers with the new resins is substantially more cost-effective for production.
“The printed parts cost 25% less to print on Form 4L than when we were printing on the Form 3Ls. That's a combination of lower material cost and higher speeds.” Rick Beddoe, Principal Engineer/CEO, Steam Factory Design and Development
Scaling Up
Now that Steam Factory is reliably producing the vRad® Grip, vRad® is looking at adding features. 3D printing means this is easy compared to injection molding. Beddoe says, “We can add additional buttons, lights, or any other feature without interruption.”
In addition to continuing to develop the vRad® Grip, Beddoe is scaling up Steam Factory, adding a location near the University of Minnesota Twin Cities campus to provide 3D printing services, seminars, and classes to students and researchers.
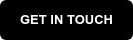