Partnering with Nexa3D and utilizing the XiP desktop 3D Printer and Freeform Injection Molding (FIM) process to produce 3D printed tools, Alpine is able to drastically reduce both their prototype tooling production times and costs in order to put parts in the hands of their customers for swift validation, testing, and customer acceptance before making large investments in permanent tools.
Original Source - Nexa3D
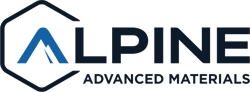
The Customer
Alpine Advanced Materials, a leading expert in the design and manufacturing of custom-engineered parts for the world’s most demanding aerospace, defence, energy, space, and transportation applications, sought to overcome the challenges associated with traditional metal parts. By introducing high-performance injection moulded composites that are significantly lighter than metal yet equally as strong, Alpine is able to provide scalable and flexible manufacturing services that are more economical and environmentally conscious as well.
INDUSTRY
Alpine Advanced Materials
PRODUCTS
XiP Desktop 3D Printer
xMOLD 3D printed tooling resin
APPLICATION
3D Printed Tooling
ADVANTAGES
- Ability to offer injection moulding services in as fast as 10 days
- Significantly reduced production costs
- Enhanced strength and surface finish
- De-risked material innovation
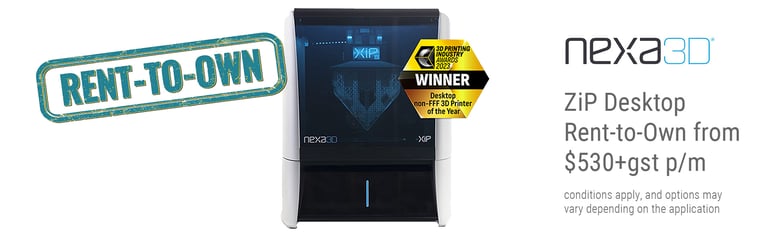
The Challenge
Conventional tooling is too costly and has long lead times
For Alpine Advanced Materials, the conventional injection moulding approach required significant upfront investment in permanent steel tooling, hindering the ability to rapidly produce prototype parts for testing and validation in key high-performance materials like HX5®, a multi-scale reinforced polymer with exceptional performance over a wide range of temperatures and extreme environmental conditions.
Additionally, standard 3D printing had proven too costly and it couldn’t withstand the high molding temperatures of their composite polymers.
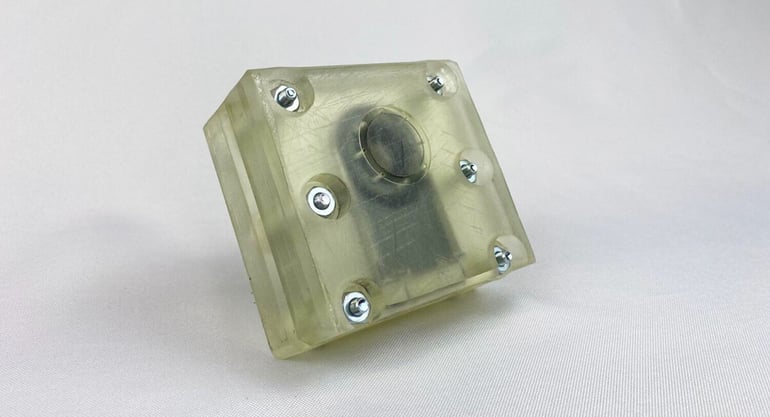
“Our customers are using the FIM process to de-risk the path to new thermoplastic materials. Rapidly molded prototypes are being used for validation testing, product demonstration and even low-rate initial production.” - Jeremy Smith, Alpine Advanced Materials
The Solution
3D printed tooling using xMOLD and Freeform Injection Molding
Recognising the potential of additive manufacturing, Alpine Advanced Materials decided to integrate Nexa3D’s XiP 3D Printer into their operation. The XiP printer, along with Nexa3D’s xMOLD resin, offered Alpine the ideal solution for their injection moulding needs. Freeform Injection Molding (FIM) with xMOLD allowed them to overcome the challenges associated with traditional metal tooling, providing a faster and more cost-effective way to produce prototype parts for customer validation. The resin’s compatibility with hundreds of plastics provided the versatile solution Alpine needed to ensure they could mold for a myriad of commercial applications.
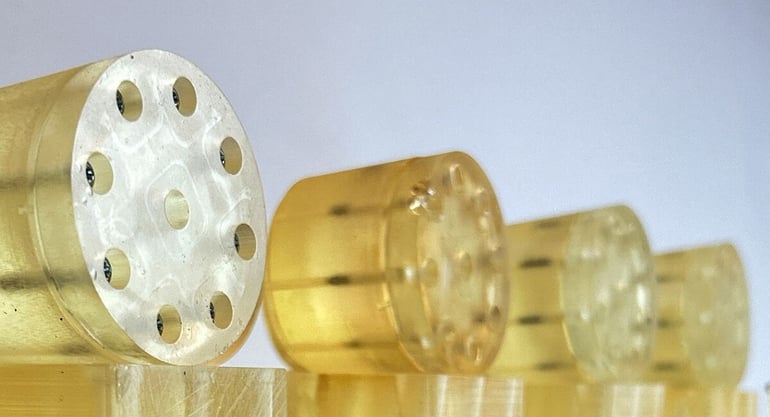
“XiP works really fast, like nothing we have ever seen anywhere on the market and at the same time offers high precision prints which is crucial in the in-ear industry.” - Jesper Anderson, CEO at earfab
The Benefit
Reduced production costs by as much as 86% and lead time by as much as 91%
By adopting the FIM process using Nexa3D’s XiP 3D printer and xMOLD material, Alpine Advanced Materials reaped numerous benefits:
Rapid Prototyping:
FIM enabled Alpine to quickly produce high-quality prototype parts for customer demonstration and validation testing. The mechanical properties of FIM parts closely matched those produced with permanent steel tools, ensuring accurate performance evaluation.
Enhanced Strength and Surface Finish:
Compared to parts directly 3D printed, parts moulded with FIM exhibited superior strength and surface finish. This made them suitable for a wide range of applications, including product demonstrations and low-rate initial production.
Time and Cost Savings:
FIM drastically reduced the time and cost required for tooling production. The XiP printer’s exceptional speed allowed for the creation of multiple moulds per hour, surpassing the capabilities of traditional CNC machining. Alpine could produce 5-10 prototype moulds for a fraction of the cost of a production tool, delivering significant savings to their customers.
De-risking Material Innovation:
FIM enabled Alpine’s customers to de-risk the path to new thermoplastic materials. Rapidly moulded prototypes provided the opportunity for comprehensive validation testing, ensuring the successful adoption of innovative materials.
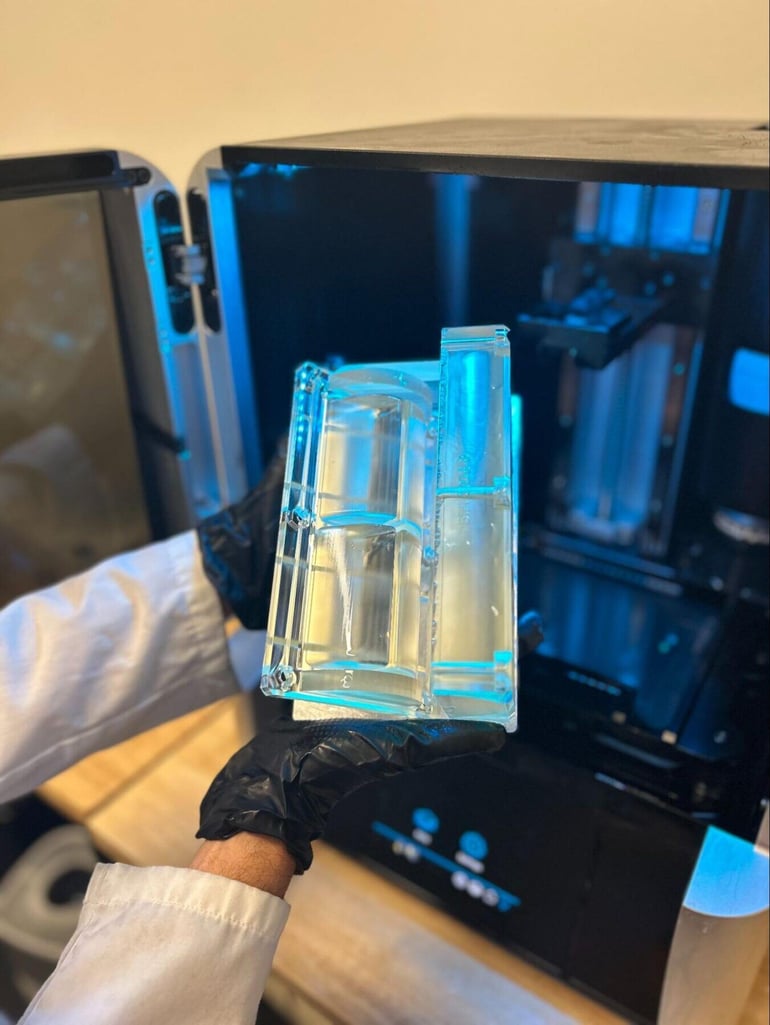
Customer Impact
Custom tool and parts delivered in 10 days saving thousands in tooling costs
A defense firm in Huntsville, AL approached Alpine Advanced Materials for rapid parts to perform a UAV system demonstration. The firm required parts with higher strength than those achievable through traditional 3D printing methods, but their metal machining capacity was overwhelmed. Leveraging FIM, Alpine designed, printed, moulded, and delivered all 60 required parts within just 10 business days, meeting the tight three-week timeframe and ensuring the successful completion of the demonstration.
The collaboration between Alpine Advanced Materials and Nexa3D has created unlimited possibilities for the manufacturing industry through the integration of 3D printing and Freeform Injection Molding. By leveraging Nexa3D’s XiP 3D Printer and xMOLD material, Alpine has successfully addressed the challenges associated with traditional metal tools. The FIM process has enabled Alpine to deliver rapid prototypes, comparatively enhance part strength and surface finish, and achieve significant time and cost savings.
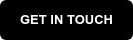