The 40-year-old Newcastle-based company specialises in the mining and tunnelling space and has been using entry level desktop MDF 3D printers for the last decade. Its customers include many of mining’s big names, such as Glencore, BMA, Anglo American, Centennial, Peabody, Yancoal and BHP Billiton.
Original Source - Industry Update
The Customer
Business Improvement Manager Callan Boslem said they were primarily used for prototyping. The move to invest in a suite of Markforged industrial 3D printers came down to two main reasons.
“It was to keep the company flexible and ensure bespoke manufacturing remains a number one focus as the business grows,” he said.
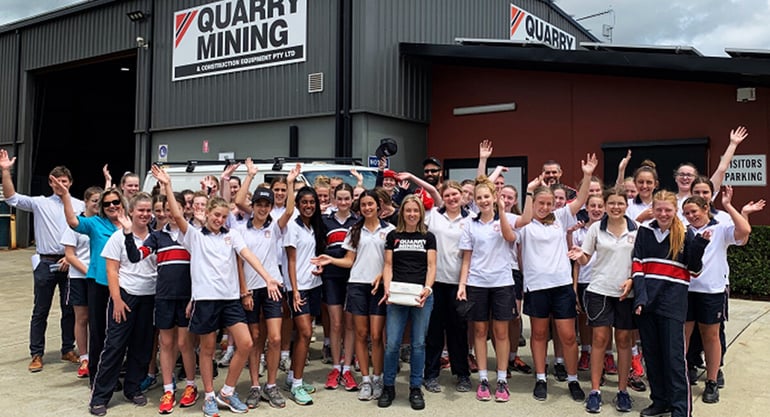
“Also, our production line is set up for bulk production, when we have small changes to a design or its low volume, it really affects our ability to manufacture efficiently. Additive manufacturing is a nice way to combat that when we need to do small run jobs or R&D jobs or one-offs from clients. It allows us to go straight from the engineering department to final production.”
The Solution
Boslem believes the strength of 3D printing is that it allows Quarry Mining to be solutions-focused.
“We are using this system so that if a customer has a specific or niche requirement, we can use our entire product suite to supply a solution, whether it’s 3D printed, traditional subtractive manufacturing or a fabricated component,” he said. This gives us an option to be the end-to-end solutions provider for clients. It gives us another level of capability, seeing as our competitors haven’t invested in it. “It allows us to maintain that solutions provider role for clients who come to us when they have problems other companies can’t solve.”
Quarry Mining engaged CBTech to install the Markforged suite of printers. The FX20 is used for large production composites, the FX7 for smaller level short-run prototyping and two Metal X printers, wash and sinter. “We’ve had a relationship with CBTech for a number of years, primarily through our IT requirements. They talked to us a few times to introduce Markforged but up until the last 12 months we didn’t have the requirement to push us over that tipping point for the level of investment required,” Boslem said. One of the reasons they went with CBTech and Markforged was the end-to-end capabilities.
“Their system includes their own software, printers and filaments. Everything that is used in the products is controlled from start to finish,” Boslem said. “From a security perspective, not having a third party was a massive benefit to us.“We also knew it was a tried and tested product, because of their contracts with military and multinationals. They have the history there to support claims that they make a high end product. For us, we needed that guarantee that our $1m plus investment will equate to a system that will do as it says.”
The Benefits
Australia has strict regulatory requirements for mining equipment, which is another reason Quarry Mining chose Markforged. "Any sort of plastic-related product in the underground coal space has tight compliance standards for what can become an ignition source. Some of the composite materials Markforged offered already had certification attached to them to make FRAS certification an option,” Boslem said. "There’s no automatic compliance in the mining industry, but the products are certainly anti-static and fire resistant, which tick compliance boxes so we are on the road to certification.”
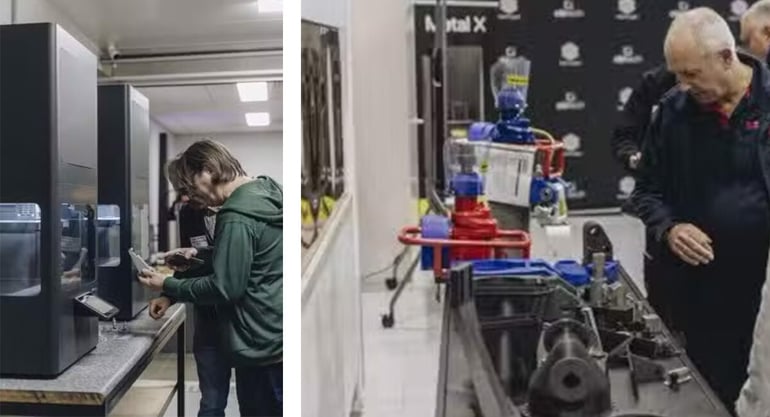
The ROI
Quarry Mining had the printers installed in April and Boslem said that just eight weeks later, it is starting to see a positive ROI.
“Like all investments, it was a bit of an educated gamble. We broke our investment into a couple of areas, metal and composite. We’ve been printing with plastics for a long time, so we hit the ground running with that one,” he said.
“The Metal X side of things was a less educated guess, I think it will be a six month process to feel our way through this learning phase. “We are already seeing quite a lot of interest from a range of customers, the majority not being in the mining space, such as the building industry or universities. “A number of projects internally using additive manufacturing are showing early signs of being quite positive from a direct reduction in production costs. Other value adds include allowing us to produce our parts in a way to have additional cost benefits, in that we can make our parts lighter, in different shapes and designs. You can’t do that from traditional subtractive manufacturing.
“I believe this gives us a competitive edge on a market we already have, and the technology will continue to evolve. We’re already seeing additional investment from Markforged in new R&D, so in 12 months we’ll be able to do more with those same printers. It’s a unique investment structure for us — we pay for an outcome, but in 12 months that outcome will evolve and not cost us any extra.”

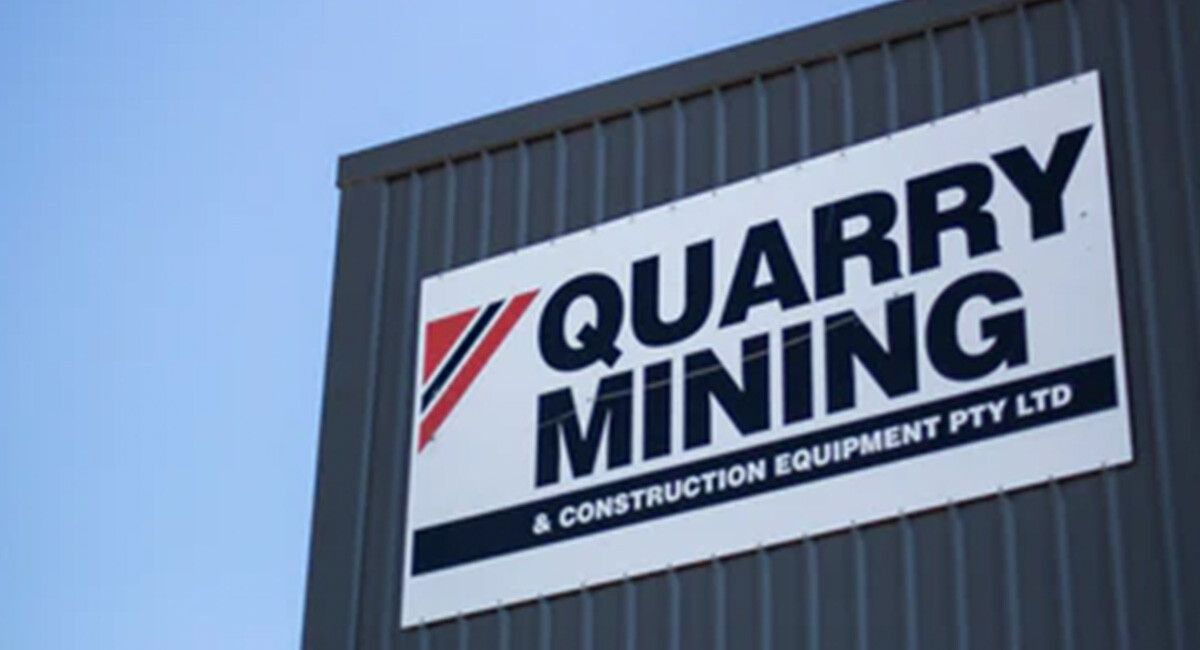