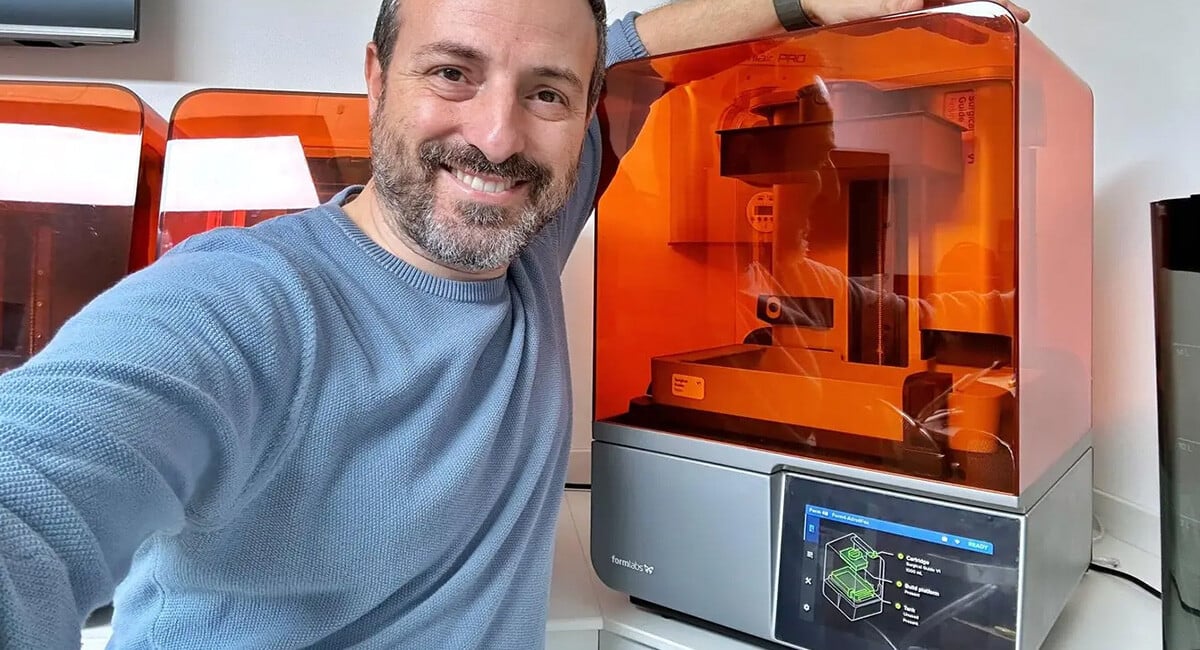

FormLabs | Digital Prosthodontics
Dr. Antonino Cacioppo is a digital dentistry expert who’s been 3D printing for almost a decade, and practicing digital dentistry since 2005. A dentist, private practitioner, and prosthodontist in Palermo, Italy, Dr. Cacioppo started out with a Form 2 3D printer, and currently uses 23 3D printers from different manufacturers, including all of Formlabs’ Form Series 3D printers for dental applications.
“You can be the best digital dentist in the world, but when you put your gloves on you need to be fast and you need technology that is easy. You don't need tons of parameters, you need the perfect ones for each resin, each application. And you need to know that you can trust your technology. Today I can say that I trust 100 percent Formlabs 3D printers. It's not the same with other 3D printers.” - Dr. Antonino Cacioppo, DDS, PhD, Prosthodontist
Each of Dr. Cacioppo’s printers is dedicated to a specific application based on his requirements for those applications and the parameters of the printers. The precision, accuracy, and reliability of Formlabs printers paired with the expansive material library have led Dr. Cacioppo to reserve Formlabs printers for biocompatible applications where high levels of precision and accuracy are needed. Printing surgical guides, occlusal splints, and both temporary and permanent restorations, Dr. Cacioppo is a 3D printing expert at the cutting edge of digital prosthodontics.
Starting With Surgical Guides
Dr. Cacioppo is a Formlabs beta-tester and KOL who started designing dental appliances for 3D printing in 2007. As an early adopter of 3D printing, Dr. Cacioppo has first-hand experience with the history of 3D printers and resins for dental applications. In 2015, he brought printing in-house with Form 2, saying, “Previously, 3D printers were not accessible, both due to their dimensions and costs. I started with a few models and with surgical guides.”
Models are the easiest application to print, but while surgical guides are also a good first application to bring in-house, they require highly precise printing to ensure the fastest, most successful procedures and outcomes for the patient. Most recently, Dr. Cacioppo has been printing on Form 4B with Surgical Guide Resin, a combination he says is “maybe the best I’ve ever used.”
“What is absolutely amazing with Form 4B is the accuracy of the printing. Because the perception is that the prints are near to zero deviation, zero error between the CAD file and the 3D print. And I can assure you that it is not a common experience with other printers. The fit with the sleeves, it's absolutely amazing.” - Dr. Antonino Cacioppo, DDS, PhD, Prosthodontist
Using Surgical Guide Resin on Form 4B, Dr. Cacioppo noted that he could not see the layers, and that the transparency and hardness were even more noticeable compared to parts printed on Form 3B+. The sleeves, too, fit perfectly on the first try.
“What is important to me is the finishing, I feel that I don't need to finish my piece. This was my first reaction with the first printed surgical guide with Form 4B.” - Dr. Antonino Cacioppo, DDS, PhD, Prosthodontist
Not needing to finish prints saves valuable workflow time, translating to less labor, cost-savings, and the difference between multiple appointments and same-day procedures. The benefits go beyond these savings, making for less chairtime, more precise surgery, and a better patient experience.
“In the future, I think that guided surgery will be the secret for all implantology, thanks to the speed and accuracy of 3D printing in-house.” - Dr. Antonino Cacioppo, DDS, PhD, Prosthodontist
But it’s not just about workflows: the final dental appliance must meet the exacting standards of dental professionals. When evaluating a new printer, Dr. Cacioppo puts it through a thorough testing regime to check accuracy, reliability, precision, and material quality.
Form 4 Series printers print with 95% of the surface within 50 μm of the CAD model, and 99% of the surface within 100 μm of the CAD model, for sleeves that fit in surgical guides, restorations with titanium bases, and appliances that fit every time.
Biocompatible, Validated Materials for Easy Printing and Predictable Outcomes
The requirements of MDR in Europe mean 3D printing biocompatible parts is carefully regulated, and Dr. Cacioppo prints all of his biocompatible resins in one room — all on Formlabs printers: his original Form 2, three Form 3B 3D printers, one Form 3B+, and one Form 4B. He uses these Formlabs printers for surgical guides, temporary restorations, long-term or permanent crowns, bridges, and occlusal splints.
The clarity of occlusal splints printed with Dental LT Comfort Resin means minimal polishing is needed.
Of these printers, two are for occlusal splints: one prints Dental LT Clear Resin (V2) for rigid splints, and one Dental LT Comfort, for flexible splints. Another printer is dedicated to printing surgical guides with Surgical Guide Resin, and Form 4B prints restorations with Premium Teeth Resin and BEGO™ VarseoSmileⓇ TriniQⓇ Resin.
Formlabs resins for biocompatible dental applications are manufactured at our FDA-registered facility in Ohio. These materials are designed and manufactured within our robust Quality Management System that is ISO 13485 and EU MDR certified. A dedicated team of operators and quality assurance professionals make the resins inside a certified ISO Class 8 clean room. All of our Medical Device Resins are appropriately registered with the FDA and CE-marked according to the EU MDR.
These strict quality standards are important for Dr. Cacioppo, even more so since Formlabs’ resins are validated on Formlabs printers, giving him peace of mind, and making it easy to press print knowing the printer settings don’t require any troubleshooting or adjustment.
Premium Teeth Resin: Similar to Milled PMMA
“Form 4B with Premium Teeth Resin was mind-blowing, because the first 3D print of a screwed-in implant-supported crown was perfect. I didn't have any sort of corrections with offsets. There was no need to manage the space for the cement. It was mind-blowing.” - Dr. Antonino Cacioppo, DDS, PhD, Prosthodontist
Premium Teeth Resin is a nano-ceramic filled biocompatible material for 3D printing of denture teeth, temporary full-arch implant-supported restorations (All-on-X appliances), temporary single units (crowns, inlays, onlays, and veneers), and up to seven-unit bridges. Dr. Cacioppo compares the appliances printed with Premium Teeth Resin as “More similar to the milled PMMA that I ever saw in my entire life. And trust me, the milling machine PMMA material is one of my favorite materials of all time — and, like me, maybe 99% of prosthodontists.”
The accuracy of Form 4B makes it possible to print screwed-in implant-supported crowns without corrections.
The similarities of flexural strength and aesthetics between Premium Teeth Resin and PMMA make Premium Teeth Resin a “game changer” when printed on Form 4B. Unlike a milling machine, which can only manufacture one crown at a time, Form 4B can print an entire build platform of restorations in the same amount of time, and the speed of 3D printing only continues to improve.
Dr. Cacioppo adds that “The supports are very, very easy to cut. They are smaller and I can choose five or six supports for each crown and everything else is clean.” This cuts down on post-processing time which, Dr. Cacioppo says, is “absolutely related to time management. All the procedures after 3D printing are related to your work, or an assistant, and time saving is absolutely important.”
Permanent Restorations: BEGO VarseoSmile TriniQ Resin & the Role of Dental Labs
Though Dr. Cacioppo has a fleet of 3D printers, he doesn’t produce all appliances in-house; the dental lab is still an important partner. Occlusal splints, surgical guides, and temporary restorations are all produced in-house, but about 40% of permanent restorations are still produced in a dental lab. Restorations made from zirconia, which requires advanced skills to mill, and final ceramic structures, which Dr. Cacioppo calls a dental art, are sent to the dental lab, to be manufactured by specialists.
Dr. Cacioppo sees prosthodontists being more and more involved in 3D printing, managing all design and production of temporary restorations in-house, with highly specialized final restorations being produced by the dental lab. This gives prosthodontists full control and quicker turnaround on temporary restorations, for faster delivery which impacts patient care, while letting the dental lab specialists produce high-quality permanent restorations.
With new dental materials becoming available indicated for permanent and temporary restorations, clinicians are slowly starting to 3D print these parts in-house for some of their cases. Dr. Cacioppo has been printing crowns, onlays, anterior bridges, and posterior three-unit bridges with BEGO VarseoSmile TriniQ Resin. Based on his use thus far, Dr. Cacioppo says it’s, “perfect for posterior implant crowns, for inlays, onlays, and overlays, and very good for long-lasting provisionals.” Additionally, he found the interaction with the cement agent to be advantageous.
“I will suggest all my 3D printing digital colleagues try BEGO VarseoSmile TriniQ Resin as soon as possible. A very good weapon in our arsenal.” - Dr. Antonino Cacioppo, DDS, PhD, Prosthodontist
Dr. Cacioppo appreciates that restorations printed with BEGO VarseoSmile TriniQ Resin are radiopaque, making them clinically visible on X-rays. However, in accordance with ISO standards, its radiopacity is below the specified threshold.
Control of Your 3D Printer Fleet: Formlabs Dashboard
“3D printing in the dental office, it's not possible if you own just one 3D printer,” says Dr. Cacioppo. While it’s easy to do material changeovers on Formlabs 3D printers, offices that are printing multiple applications a day will find it easier to have dedicated printers for each resin.
“It's not related to the printer,” says Dr. Cacioppo. “But when, every day, you’re printing occlusal splints, temporaries, models, and surgical guides, your dental office needs more than one printer.”
“There is the world of dental 3D printing and then there is Formlabs. When you have multiple 3D printers — and this is the future for dental — you need a good way to manage all those 3D printers. And there is nothing close to the Dashboard and the ecosystem from Formlabs.” - Dr. Antonino Cacioppo, DDS, PhD, Prosthodontist
Dr. Cacioppo relies on Dashboard to monitor and manage printers. “I love Dashboard because my secretary and my assistant know the printing time and if everything is okay. Lots of times I am out of my office for courses or congresses. If I want to print something, I can print even if I’m outside of my office.” Everyone on staff can track prints, get notifications about print status, and start jobs from anywhere. Dashboard also tracks material usage for seamless reordering.
Good for Patients & Practitioners
“The speed of new 3D printers is a good thing — it’s a good future for the patients. For example, prosthodontists could have the ability to have three different shapes of the same tooth of the same patient, and you can try one after another for an aesthetic visualization.” - Dr. Antonino Cacioppo, DDS, PhD, Prosthodontist
The technology powering Formlabs Dental 3D printers makes printing easy and intuitive while empowering the production of a full range of appliances and restorations.