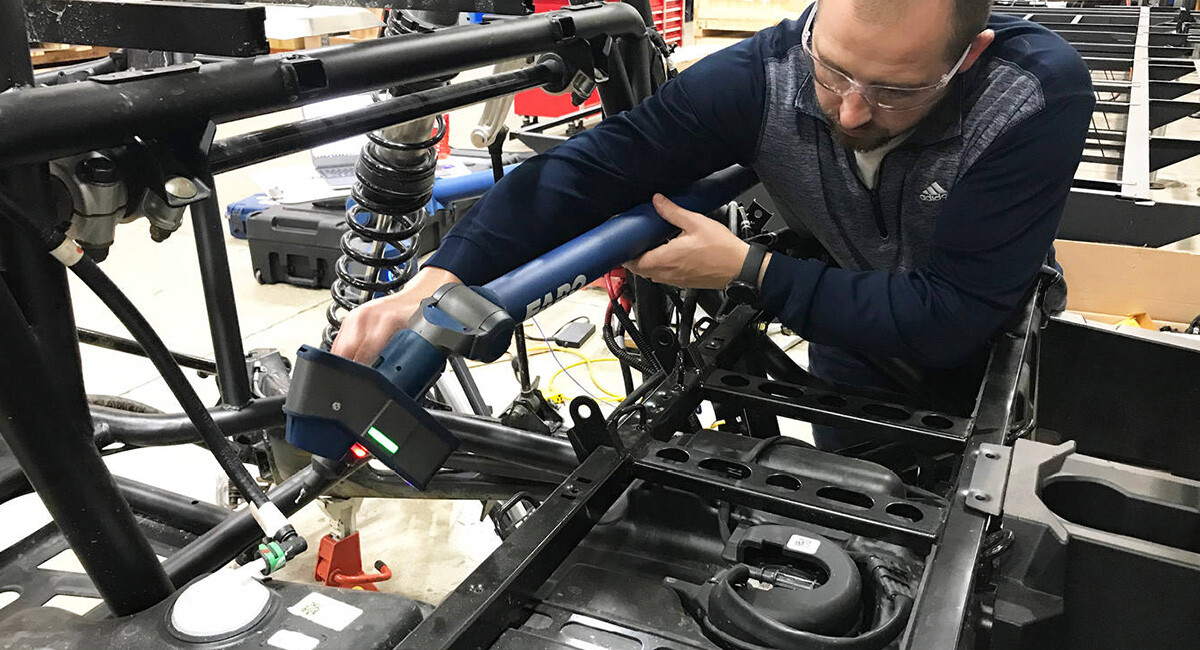

FARO | Pratt Miller Reverse Engineering
How Vehicle Design Juggernaut Pratt Miller Uses 3D Scanning and Probing to Help Supercharge the Maturing Electric Vehicle Market
The Challenge
In August 2020, an article in Protocol, a tech news website launched by former Politico owner and publisher Robert Allbritton, declared that after years of gaining background momentum, 2023 would, finally, be the year of the electric vehicle.
At the time, the article noted a variety of trends enabling this near-future breakout year: a pledge by several nations and US states to wean their drivers off internal combustion engines in light of the growing climate crisis, (Canada was arguably the most bold with its goal to achieve 100% zero-emission vehicle sales by 2040), the predicted growth of EV manufacturers other than Telsa, and continued advances in the global charging, energy storage and transmission network.
Nearly four years later and it seems as if Protocol’s prediction is proving prophetic. More nations have committed to phasing out the sale of ICE vehicles, in the US EV sales are up 48.8% year over year in the"second quarter of 2023, and price cuts combined with tax incentives are, for the first time, placing these vehicles within reach of ordinary consumers for under $40,000. But for this vehicular transformation to continue, plenty of behind-the-scenes innovation must go on. That’s where engineering juggernaut Pratt Miller comes into play, thanks to its reliance on reverse engineering and the FARO® Quantum Max FaroArm®, the world’s leading portable coordinate measuring machine (PCMM).
Headquartered in New Hudson, Michigan, a Detroit suburb, the groundbreaking engineering and product development company uses 3D scanning and probing technology to build methods of transportation for the motorsports, defense and robotics industries. One of the company’s latest areas of expertise includes designs for what it calls the “new mobility” market, specifically as it relates to electrification and EV startups. New mobility in this context speaks to any ground vehicle that’s not defence or motorsports-related, robotic or manned platforms, with a heavy focus on EV and fuel cell powertrain integration and hybridization.
Known as one of the most innovative product development and technology integration companies in the world, the Pratt Miller team specifies, designs, integrates and fabricates all the necessary components for electrified driveline systems, including mature control algorithms and software for optimal system performance.
‘Fuel the Mule:’ Designing What Works
Recently, Frank Wilson, Senior Quality Manager at Pratt Miller, sat down with FARO for an interview to discuss exactly how reverse engineering factors into vehicle design development and how the Quantum Max FaroArm boosted the company’s speedy completion of new projects, along with significant gains in parts accuracy and precision measurement.
Most often Wilson and his teamwork with what’s known in the industry as “mules,” or “development mules,” which are test bed vehicles fitted with prototype parts. Before a vehicle can enter mass production, or even pre-production, it must first be evaluated at this preliminary stage. Sometimes a development mule can be years away from the actual assembly line. And by then, many design features may have changed. Test bed vehicles like this are often constructed with off-the-shelf parts — parts that lack their design specifications, dimensions and basic geometry.
3D metrology technology like the Quantum Max offers a contact and non-contact measurement solution to obtain this information in real time and without the need for a bulkier, costlier, more specialised training required from a coordinate measuring machine (CMM). By measuring the dimensions of an off-the- shelf part, companies like Pratt Miller can begin
to fit all the disparate parts together into a single, functional test bed vehicle for their customers. Then, Pratt Miller can evaluate vehicle dynamics, including suspension geometry and road load wheel forces, to ensure the testbed and the machinery it contains is a safe, reliable pre-prototype test platform.
“So, we’re basically integrating the guts that our customers want to test into some other vehicle that’s not theirs, versus on the defense side when we’re" "often reverse engineering existing vehicles where CAD data is unavailable to integrate new technologies into fielded platforms,” Wilson explained. “Both laser and hard point scanning with the Quantum Max are performed on the actual frame. That includes the chassis and the entire vehicle body on frame.”
Once off-the-shelf parts are measured, spatially aligned and fitted onto the mule, the complete vehicle is 3D laser scanned in order to create a CAD model of the design. This is the heart of what reverse engineering is all about. Instead of working with a CAD blueprint at the start of the process, the blueprint is created after the physical prototype is made. The value of this CAD model comes later in its digital shareability with project stakeholders/managers, as well as in the future need to mass produce or pre-produce additional mules. The CAD can also be used as a reference point if the prototype mule undergoes additional design changes, which is likely.
Compared to how reverse engineering is done today, Wilson colourfully characterized working with more traditional measurement methods as a “nightmare.”
“I’ve been spoiled as I’ve always had a FARO [portable measurement] arm with a laser scanner to do reverse engineering in my 15 years here,” Wilson said. “So I know what it would take if you didn’t have something like this which is a lot of time and effort, relying on height gauges, gritting up from a bed plate, measuring, identifying your reference plane, measuring your distance. It would require a lot of calipers and hand sketching. But you can’t really capture the 3D relationships of features very well.
Now, thanks to the Quantum Max, what used to take a couple of hours or even days might only take half an hour or an hour depending on what the projects needs were.” Frank Wilson Senior Quality Manager
Quantum Leap for EVs and for Precision Measurement
One of the key insights Epps takes from working with 3D tech is its potential to simulate and refine construction workflows before breaking ground. Epps articulated the unique challenges inherent in construction projects, where each one represents a one-of-a-kind endeavor — distinct from the repetitive assembly line processes seen in other industries. While industries like automotive manufacturing have mastered the art of the assembly line through repeated iterations, construction projects unfold in unique environments with varying conditions. Each job is different.
“In construction, we know that robots are not going to be doing our jobs tomorrow. That’s not the future we’re trying to implement, and it’s not a reality,” Epps said. “But if we can chip away at a percentage of waste here and there using the 3D tools, all of a sudden, that adds up to significant savings on a project — and that’s huge.”
Wilson estimates that by using the Quantum Max, he saves about 25% per project compared to previous generation equipment. The biggest advantage, he sees, is being able to use the Quantum Max’s contact probe and three hot-swappable laser line probes that can be changed in seconds, with no need for recalibration so work can continue virtually uninterrupted and that each probe — FAROBlu xR, FAROBlu xP, and FAROBlu xS —are each designed for specific project needs, balancing maximum accuracy and resolution with speed and productivity.
Additionally, three FaroArm models offer basic, standard, and premium performance options— available in various working volumes from 2.0m to 4.0m. Improved rigidity and stability deliver optimized accuracy and repeatability with superior performance while maintaining shop-hardened ruggedness for use in the harshest factory conditions or when testing new vehicles. The new 2.0m working volume arm delivers the best accuracy in its size category.
“The portability is a huge thing when we’re having to work on vehicles across multiple facilities,” Wilson added. “That’s especially the case if you have a large military vehicle and can’t drive it on the road or a tractor trailer or something like that or a half taken apart vehicle.”
With advantages like these it’s clear the Quantum Max, used as a tool to reverse engineer off-the-shelf parts, will continue to be an invaluable tool for the burgeoning electric vehicle market, especially as the industry at large continues to gain traction with middle class consumers and the general driving public.
Already, the existing global EV market has reduced total road fuel demand by 3%, displacing 1.5 million barrels of oil used per day. While the world still has a long way to go in terms of radically reducing carbon dioxide emissions, plausible scenarios do exist to achieve net zero carbon neutrality by 2050.
Thanks to the ongoing behind-the-scenes dedication and hard work from the Pratt Miller team, just maybe a 27-year-long prediction about the future of how the human race (and its autonomous and semiautonomous robots) gets around, will be as accurate as the one Protocol made in 2020 about 2023.