Europe’s First ISO/ASTM Compliant 3D Printed Social Housing Project Completed Ahead of Schedule
Harcourt Technologies Ltd (HTL.tech), a leader in 3D construction printing based in Ireland and the UK, has successfully completed Europe’s first social housing project utilizing 3D printing technology compliant with the ISO/ASTM 52939:2023 standard. The project, located in Grange Close, Ireland, was built using COBOD International’s BOD2 3D construction printer and achieved completion in just 132 days—a 35% reduction compared to traditional construction methods that typically require over 200 days.
Original Source - 3D Printing Industry
The project featured load-bearing double cavity walls, each 10 centimeters thick, printed without reinforcement in accordance with EN206 and Eurocode 6 standards for unreinforced masonry construction. This method not only ensured structural integrity but also demonstrated significant advancements in sustainable building practices. The superstructure was completed in an impressive 12 days, highlighting the efficiency of additive manufacturing in accelerating construction timelines.
Justin Kinsella, Director of HTL.tech, emphasized the significance of this achievement: “HTL.tech is extremely proud to be the first company in Europe to build a structure that complies with the rigorous new I.S. EN ISO/ASTM 52939:2023 additive manufacturing standard. The COBOD BOD2 3D printer was crucial in this accomplishment, enabling us to complete the Grange Close Social Housing Scheme 35% faster than traditional methods.”
First Social Housing Project compliant with ISO 52939:2023 in Ireland was completed 35% faster than with conventional methods. Photo via COBOD International.
Recognition and Technological Advancements
The National Standards Authority of Ireland (NSAI) honored HTL.tech with the Standards Innovation Award for their integration of international standards into 3D construction printing processes. Geraldine Larkin, CEO of NSAI, stated, “This honour recognises HTL.tech’s exceptional integration of standards into their 3D house construction printing processes. Their innovative efforts are positioning Ireland as a leader in this field and demonstrating how standards can drive cutting-edge advancements.”
Since the project’s completion, HTL.tech has further enhanced their printing capabilities by upgrading the BOD2 printer’s concrete hose to a 65 mm variant, increasing volumetric output by 40% and reducing future printing times from 12 to just 9 days. Henrik Lund-Nielsen, General Manager and Founder of COBOD International, commended HTL.tech’s progress:
“This award is a testament not only to HTL.tech’s professionalism but also to the potential of 3D construction printing in increasing execution speed, reducing labor costs, and producing high-quality structures in line with international standards.”
Days spent on completion of the 3D printed social housing project compared to conventional methods. Photo via COBOD International.
Advancements in 3D Printing Construction Technology
This project builds on recent advancements within the 3D construction printing industry. In 2024, COBOD International introduced the BOD3, a third-generation 3D construction printer designed for large-scale, low-rise projects. The BOD3 has been deployed by Modula Tiga Dimensi in Indonesia, Power2Build in Angola, and Ab’aad 3D in Bahrain. These deployments have demonstrated the printer’s capacity to accelerate construction timelines, allowing continuous construction processes on large sites.
Additionally, researchers at the SEAM Research Center developed SEAM technology, focusing on Screw Extrusion Additive Manufacturing for construction. The Epic3D portal printer produces large-format plastic components, such as facade elements, using granulate-based materials. SEAM technology is being applied in facade manufacturing, with collaborations between Fraunhofer Institute for Machine Tools and Forming Technology (IWU) and Wirth & Co. GmbH to produce components that meet fire safety, UV, and weather resistance standards.
The SEAM Research Center: Epic3D (bottom left), METROM P1410 (center), and SEAMHex. Photo via Fraunhofer IWU.
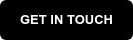