Six nerds, one invention, five continents: COBOD's Danish concrete adventure
The Danish company COBOD has developed the world's largest 3D printers, which print concrete buildings in Asia, North and South America, Africa and Europe. Behind the company are six robot nerds, who have got big players such as General Electric, Holcim and Peri on the team.
Original Source - BETON Magazine
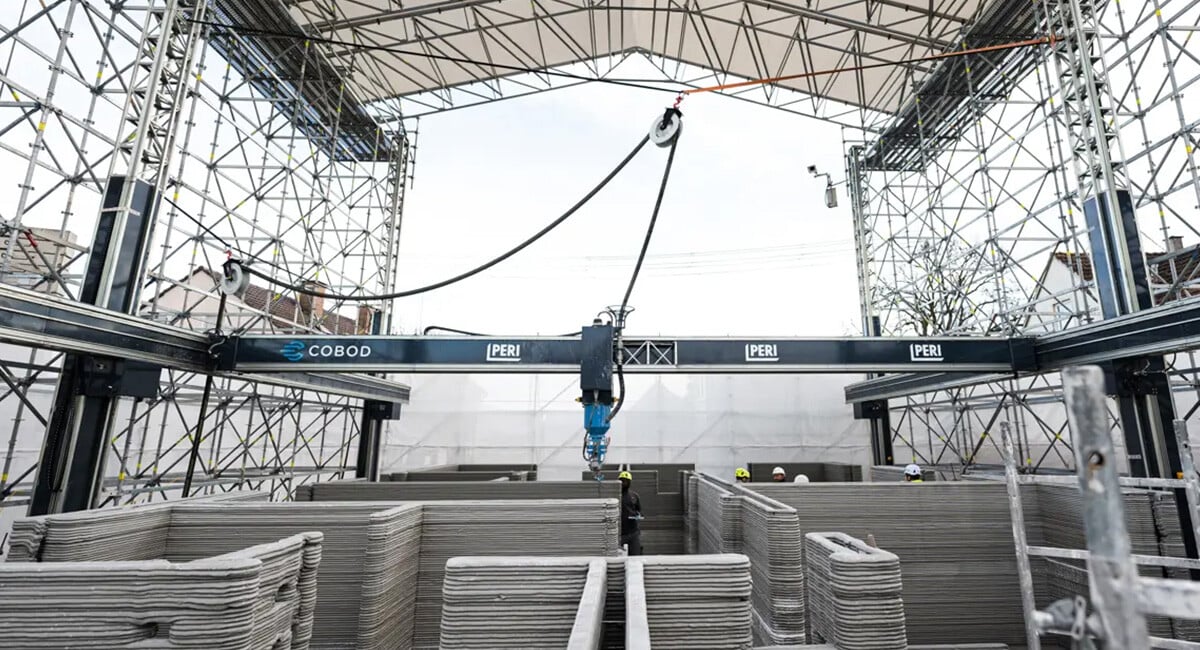
Snapshot from a 3D printing site in Germany, where Peri 3D Construction is in the process of printing a residential building.
COBOD is behind the world's largest 3D-printed building and has managed to establish itself in 40% of the global market within a few years. Behind the invention of the phenomenal printer are six robot nerds who saw the benefits of 3D technology early on and decided to conquer the construction industry.
"3D printing changes the rules of the game for the production of a wide range of goods, because you can print your product without a lot of components, subcontractors and people. We experimented with both medical implants and jewellery before we decided to develop a printer that could print buildings in concrete," says founder and CEO of COBOD Henrik Lund-Nielsen.
Freer Design
After a few years of testing and development, COBOD was ready with their first 3D construction printer in 2017. It didn't take long before Peri, Holcim, Cemex Ventures and General Electric joined the field as co-owners. For a company like General Electric, it was especially the opportunity to be able to print its own concrete wind turbine towers that attracted them, while the formwork company Peri wanted to have a foot in the competitor's camp.
"When you 3D print a building, you don't need formwork. The design becomes more free because you can print all kinds of organic shapes. At the same time, it is ultra precise and very fast to build with, so it is a completely different process than casting with formwork," says Henrik Lund-Nielsen.
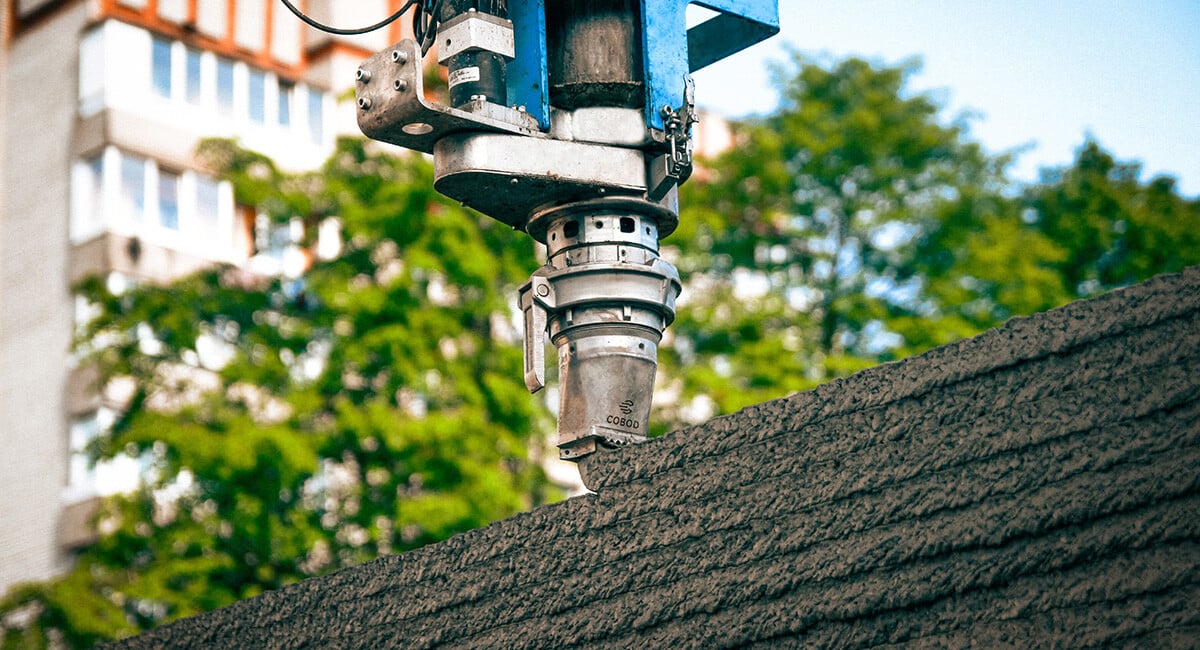
3D printing can construct buildings much faster than conventional construction, as here in Ukraine, where a new school of 370 m2 was printed in four days.
Better use of concrete
3D printing is especially good for warehouses, data centers, wind turbine towers and water tanks. The closer it is to a shell building or a raw concrete structure, the better the technology fits at the current stage. However, the development is advancing rapidly, so the complexity of the tasks is growing month by month. COBOD also collaborates with Ramboll to develop new and better construction methods for wind turbine towers and water tanks:
"If you have a water tank that is 10 meters high, then the pressure is greatest at the bottom and least at the top. When casting in situ with formwork, you have to work with the same thickness throughout the entire way, so that the entire tank is dimensioned for the greatest pressure. Our printer can mold the water tank layer by layer and reduce the wall thickness as the pressure decreases on the structure. This saves materials and CO2," says Henrik Lund-Nielsen.
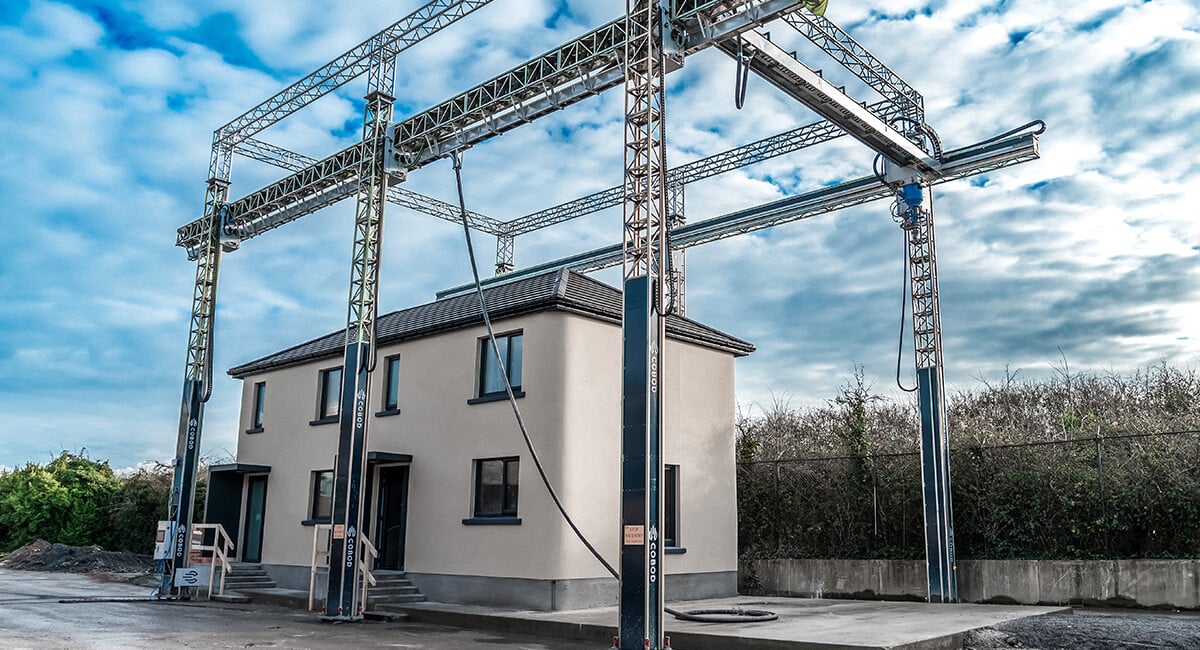
It took the company Harcourt 12 days to print the shell for a social housing building in Ireland. The building is 330 m2, on two floors and contains 3 apartments.
Robot people – Not concrete people
Today, the concrete is mostly mixed on the construction site, but in the long term, it could be good to have the concrete delivered by truck to the site. Therefore, COBOD has joined the Danish Association of Factory Concrete to learn more about the industry and get new partners:
"We are not concrete people. We are robot people, so we need networks, partners and insight into ready-mixed concrete. We look forward to learning more about the issues the industry is struggling with – not least in relation to CO2," concludes Henrik Lund-Nielsen.
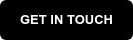